equipment
Our company has more than one hundred sets of advanced and professional production equipment, and has implemented a complete and strict quality control system in every link from raw material procurement to finished product packaging. In addition, we have passed the ISO9001: 2015 quality management system certification.
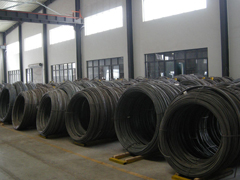
Raw materials
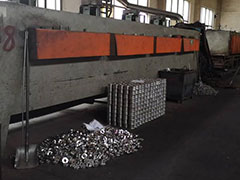
Heat treatment
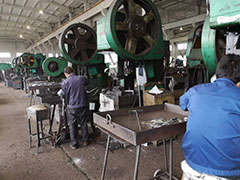
punching
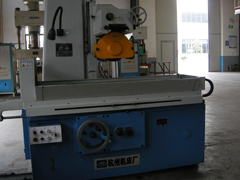
fine grinding
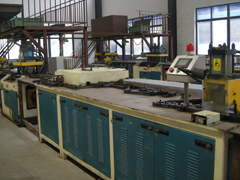
Assembly
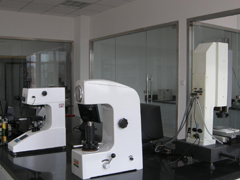
Detect
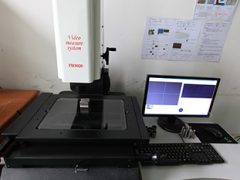
Detect
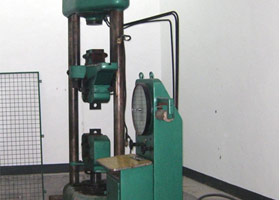
Tensile testing machine
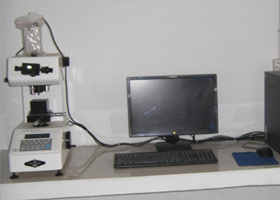
Micro Hardness Tester
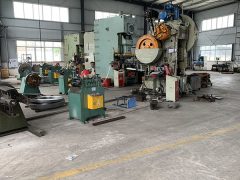
Production workshop
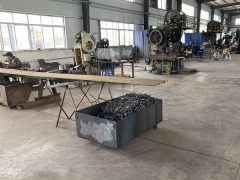
Production workshop
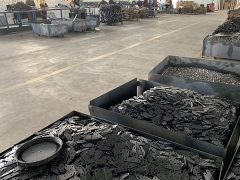
Production workshop
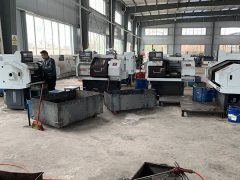
Production workshop

Welding workshop
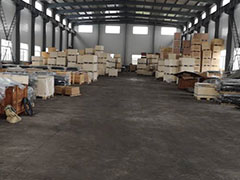
warehouse
quality assurance
From raw materials to production to finished products, every step is strictly tested to ensure the quality and reliability of the products.
1. Material inspection
- When purchasing raw materials, we will require steel suppliers to provide steel quality certificates and steel tables.
- Carry out sampling tests on materials.
- Only qualified materials are allowed to be put into the warehouse, and then cold rolled and cut to achieve the ideal state of manufacturing the chain.
2. Inspection of parts
- The mold development center has inspected all molds before use.
- The operator checks the chain parts from time to time during the production process.
- The quality supervisor continuously inspects the workshop parts.
- The operator performs anti-rust treatment on all parts.
- The person in charge of quality inspects the mold every hour to ensure the accuracy of the mold.
3. Heat treatment
- Advanced heat treatment equipment ensures the high quality and stable characteristics of all chain parts. And all necessary data during the heat treatment is processed and recorded by the computer.
- The quality management personnel carefully test the hardness and carbon layer of the heat-treated chain parts, and record the results for submission to the quality control center in the future.
- Shot peening is a necessary procedure for GD chain. To a large extent, the fatigue strength and life of the chain are improved.
- All parts have undergone anti-rust treatment again.
4. Inspection during the production process
- Each assembly line is equipped with a part tester, which solves the problem of shortage of chain parts.
- The operator controls the width between the inner panels during assembly.
- Running-in.
- Short circuit test of parts.
- Surface and flexibility test.
5. Finished product inspection
- Tensile test
- Determination of chain length
- Fatigue fracture test
- Wear test
Free Estimation
Request A Quote
We are a professional chain and sprocket manufacturer and supplier. It mainly produces mechanical transmission chains and mechanical accessories. We will reply to you within 12 hours after receiving the inquiry during working days.